ABSTRACT
Red Lake is one of the world’s most prolific gold mining districts located in a remote part of Ontario, Canada. The High-Grade Zone (HGZ) has been the backbone of numerous high-profile gold mining operations. A well-known international gold miner wanted to reduce exposure to risk for its employees and increase production with the use of innovative technology in this underground gold mine. The mine’s direct focus remains on asset optimization, cost reductions, and safety.
The continued transition to mechanized mining, bulk mining, and automated material movement, enabled the company to lower operating costs and improve safety for the workforce. The mine life was also extended due to the ability to mine lower grade at a profit. This article is intended to outline the benefits of applying Hard-Line’s TeleOp and TeleOp AutoX systems.
INTRODUCTION
With current mining innovations, the mine increased development rates with operational improvements. This approach improved the utilization of equipment and personnel which increased mine production. The company’s plan to make this asset one of the safest mines in the world was made possible with the support of HARD-LINE technology.
The TeleOp system gave the operators full functionality of the machine as if they were operating the machine underground and sitting in the cab. The TeleOp Control Station was installed in a command center situated on the surface of the mine. The location removed the operators from any possible hazards associated with underground operations.
APPLICATION
HARD-LINE’s TeleOp Control Stations provided the ultimate safety, even for novice operators. It enabled the operator to control heavy equipment from a safe and ergonomic environment on the surface (or in a remote secure location). The use of TeleOp can be for any type of equipment, providing diversity, scalability and flexibility with the technology. In addition to the safety factor of the system, production rates are guaranteed to increase. The operator does not need to travel to and from the machine and can operate machinery during and right after blast cycles. As of the writing of this case study, the mine had 6 LHDs underground remotely operated from surface, with additional systems installed in the command center to control an underground locomotive and a rock breaker. The underground locomotive transports ore and waste on a dedicated tramming level. HARD-LINE’s technology enabled the mine to control the chutes that the ore is coming out of, the locomotive, and the dump into the next ore or waste pass. It can also perform these functions automatically and allows the operator to control a loader while keeping an eye on the locomotive (see figure 1).
The mine utilizes TeleOp Multi, which is an upgrade to the standard TeleOp system. The Multi upgrade allows an operator at one Control Station to have control of a pool of machinery. Changes to control layouts for different machine types is provided through a state-of-the-art software user interface, requiring a single familiar Operator Station. The integration of HARD-LINE’s technology is helping the mine minimize its operating costs by increasing the efficiencies of day-to-day duties accomplished by heavy machinery.
FEEDBACK
In an underground mining environment, the mine must be cleared to blast. This safety procedure requires the underground operation to shut down, resulting in downtime of machinery and travel from underground to surface resulting in a loss of production during those windows which account for 4-6 hours per day. The Superintendent, Operational Excellence said that the distinct advantage of the TeleOp system is that they don’t have to worry about those windows. The operators can continue working in a safe location at the surface (see figure 2).
https://www.canadianminingjournal.com/features/remote-systems-provide-safer-approach-to-mining/
Other benefits mentioned were that the mine has overall improved productivity, including mucking rates, material handling rates, even development and overall stope cycle rates because the material can move quicker. The Superintendent, Operational Excellence commented that approximately 20% of the mine’s muck is currently being moved using HARD-LINE’s technology (see figure 2).
CONCLUSION
With experience in many specialized areas, HARD-LINE continues to enhance efficiency at mine sites all over the world with expertise in line-of-sight remote operations, tele-operation, and autonomous methods. Since operator safety has been entrenched in our ethos since day one, HARD-LINE ensures that mining companies will deliver beneficial results to its stakeholders by increasing asset utilization and capturing on missed revenue opportunities while lowering operating costs and increasing production values.
For this project, higher productivity was attained with less human intervention subsequently reducing the opportunity for error. The new system ensured workers’ exposure to dust, vibration, and noise, and all of the other dangers inherently associated with working in underground mines were significantly reduced. HARD-LINE’s system provided employees with a better and safer work environment.
Figure 1. A TeleOp operator controlling an underground LHD from surface.
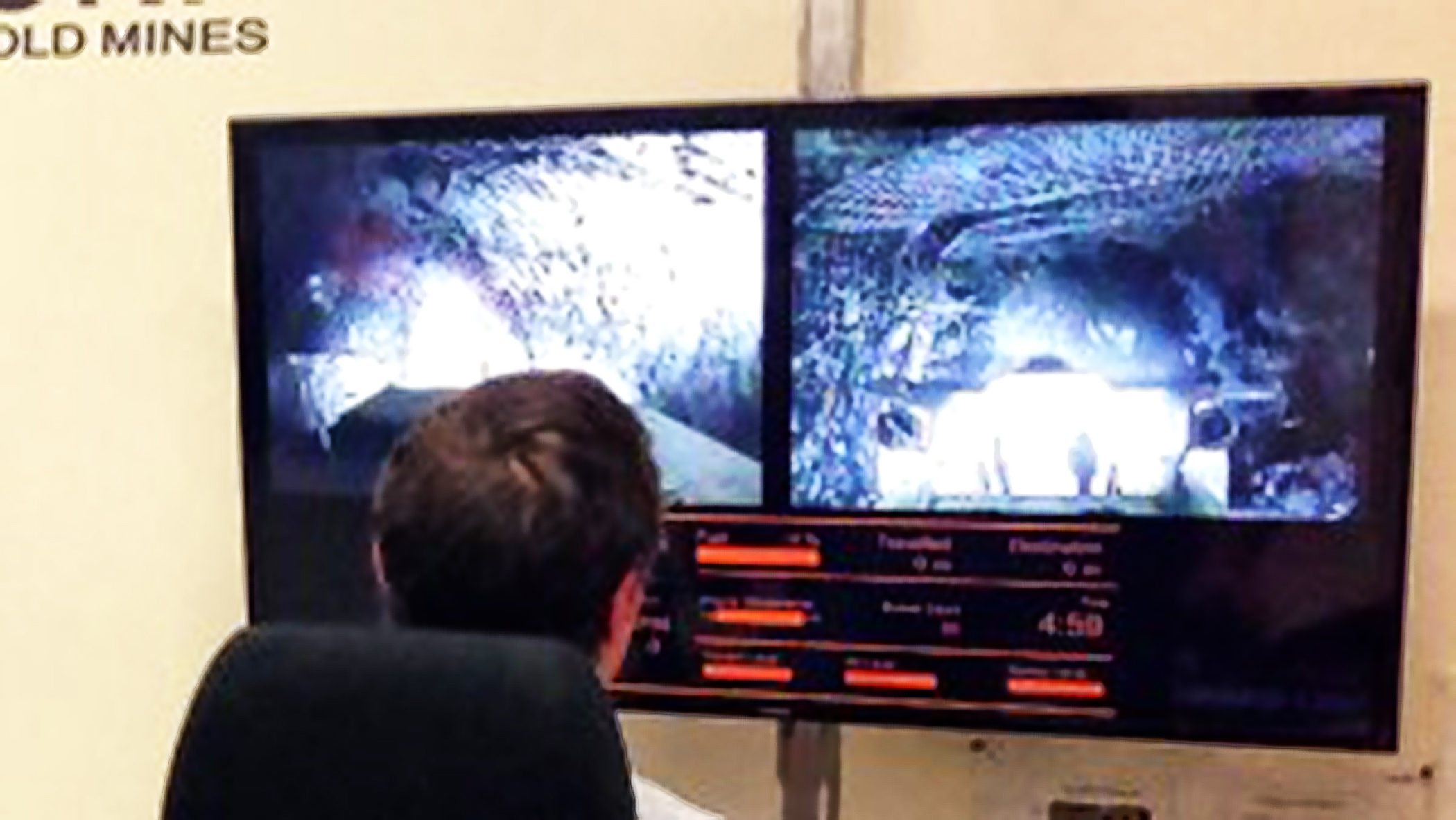
Figure 2. A TeleOp operator controlling an underground LHD from surface.
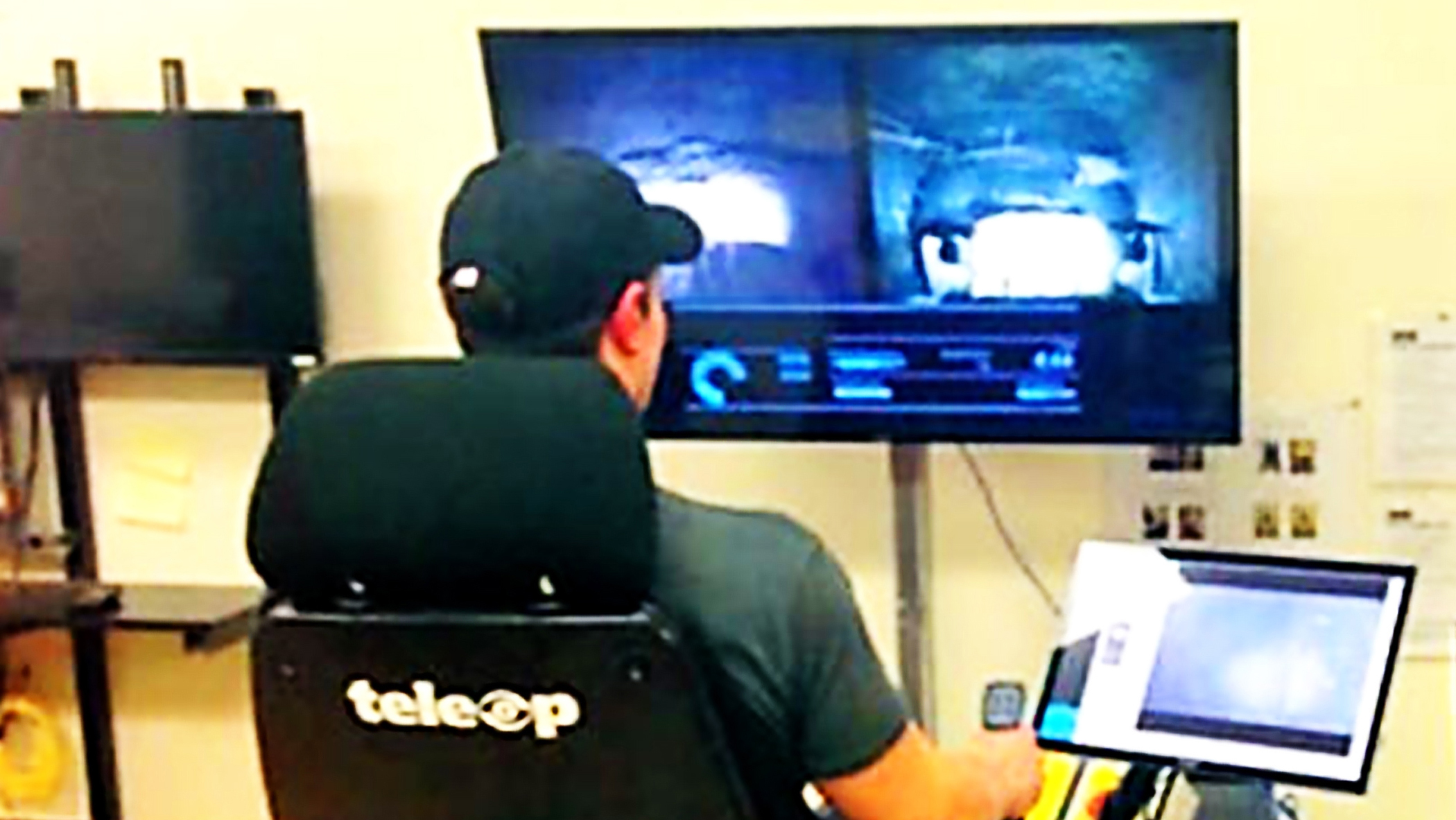
Figure 3. The control room on the surface has 5 chairs operating 6 loaders, a locomotive, and a rock breaker.
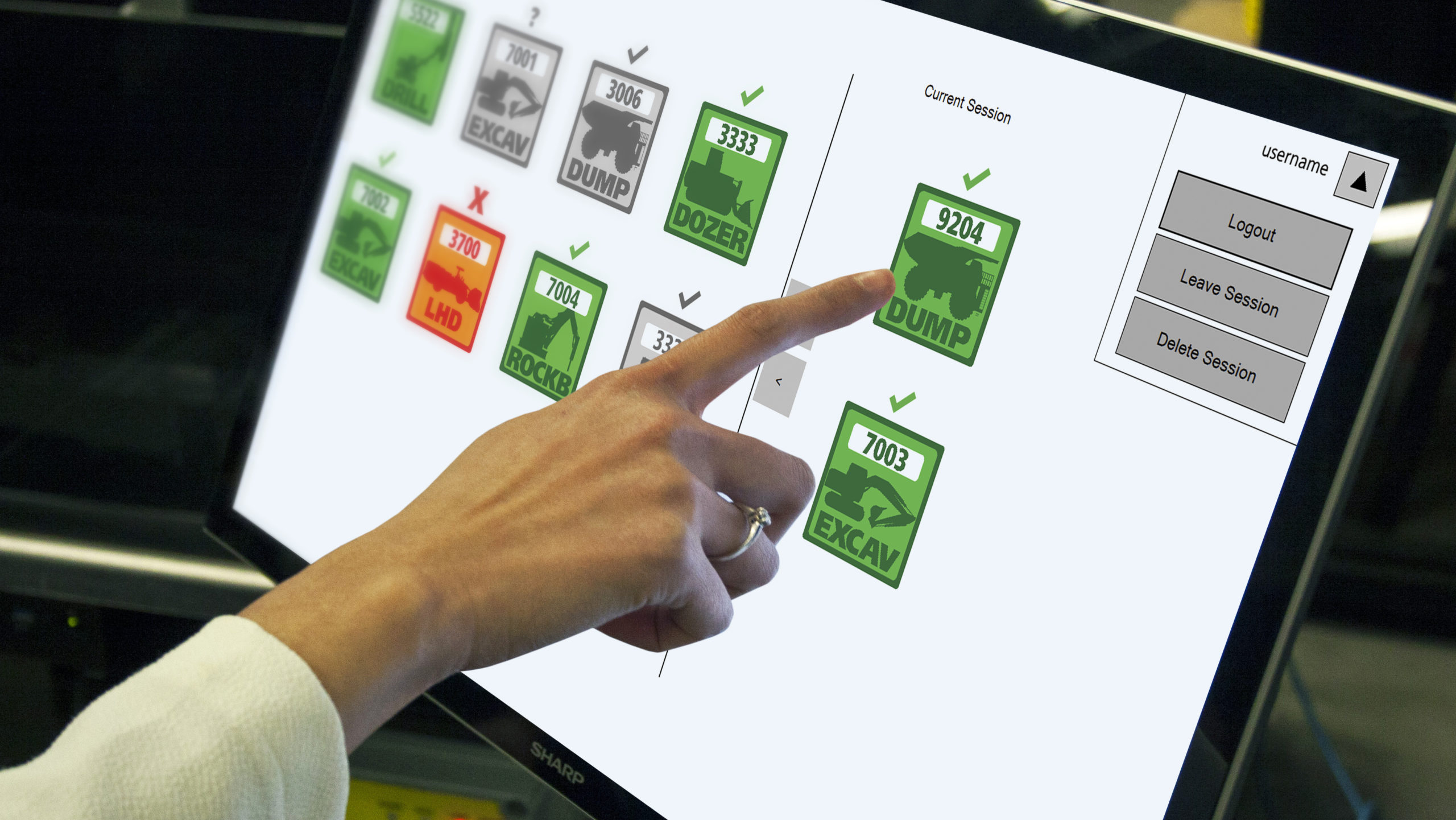
Figure 4. An LHD navigating a treacherous underground mine shaft through remote operation.
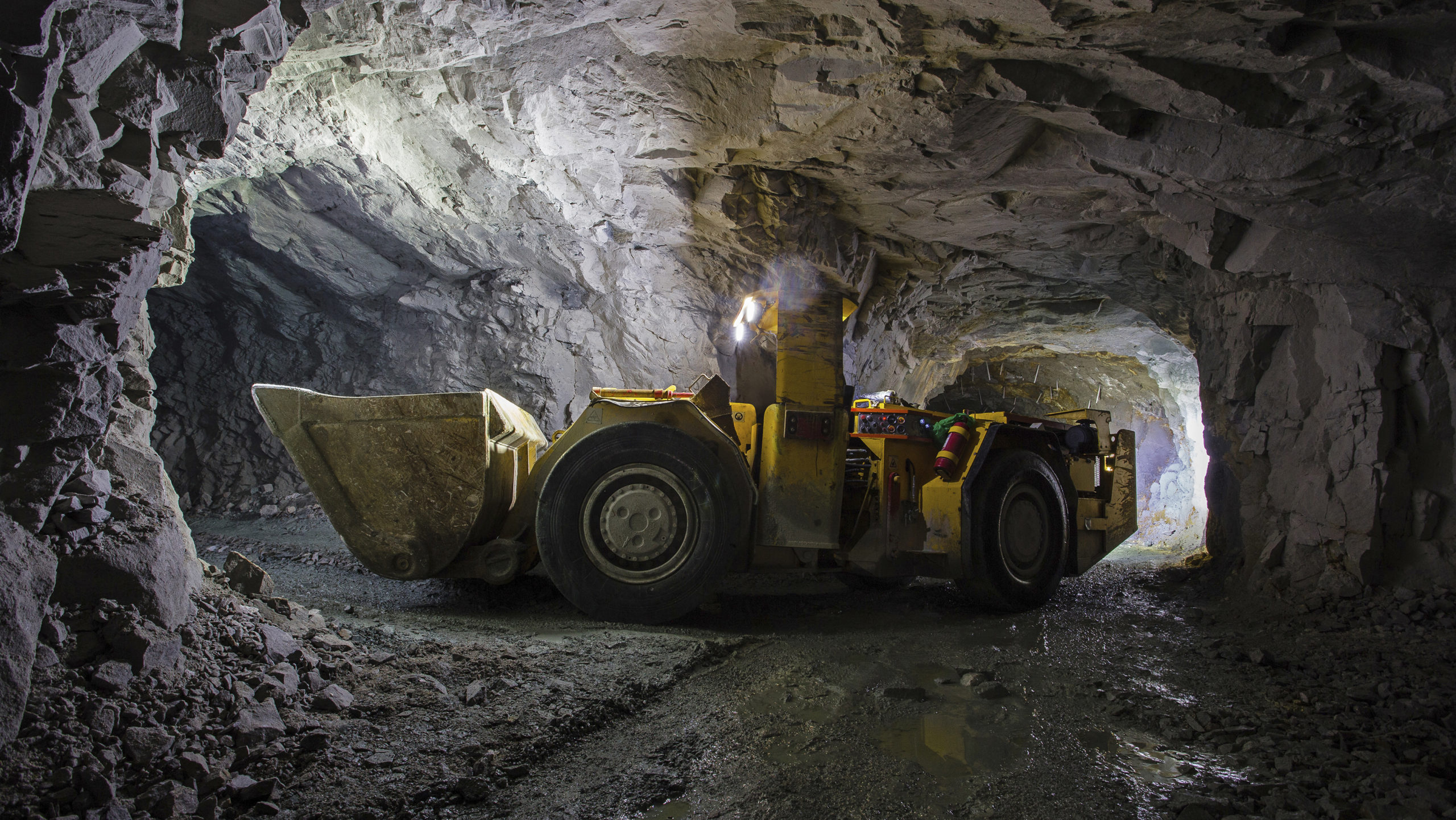