ABSTRACT
Mining companies worldwide are increasingly seeing the need to implement innovative new technologies as a solution to the various challenges they face. A leading Canadian producer of iron ore concentrate and pellets located in Labrador City, Newfoundland, is one of a number of companies that was able to complete an elaborate project using HARD-LINE technology. This company wanted to apply new strategies that mitigate safety challenges in its open pit mine. Teleoperation was applied to address these concerns. This article outlines the application of HARD-LINE’s TeleOp system for use on various projects during the mine’s operating schedule starting in 2015.
INTRODUCTION
The production process began with a drilling and blasting campaign. The crude ore was loaded onto trucks, which dumped material into loading pockets or into an in-pit crusher. The material from the crusher was directly delivered to the concentrator’s ore storage barn, known on site as the “steel barn”, via an overland conveyor system. There were multiple pieces of equipment and machinery equipped with the ability to override remote operation by taking over in local manual control. The iron producer installed HARD-LINE’s TeleOp system in the mine to address health and safety concerns in the storage barn facility. During winter months the storage barn gets frigid (average of -22°C), leaving an unpleasant environment for the workers inside. In addition, airborne particulates are generated due to the transfer of ore material and other processes. By applying a TeleOp system, exposure to this harsh environment was significantly reduced for front-line workers.
APPLICATION
The company’s procurement was for two TeleOp systems to be installed. Each system included a TeleOp operator station, monitors and cameras, which were placed in different areas of the barn, on a CAT D8 Dozer and CAT 349 Excavator. The system enables one-to-one control during operations, with no limitation on functionality. The TeleOp systems were situated in a climate-controlled office environment 7 kilometres (4.25 miles) away from the steel barn. This approach provided workers with health and safety benefits as well as enabled opportunities for increased machine utilization.
The adaptability of the TeleOp systems provided the mine additional opportunity to meet future challenges. A prime example of this was when a blast misfire prompted the need to develop the Blast Misfire Project. This project involved the handling of explosive products that remained in the rock mass after a blast misfire. Explosive products can be triggered during digging and other applications involved in the mining process; therefore, another means of handling this situation had to be considered. It was critical for the company to remove the unexploded charges and detonators to avoid possible injuries or worse, fatalities.
The flexibility of the TeleOp provided the company with safe solutions it could quickly deploy. Using the existing TeleOp dozer on the Blast Misfire Project, the system allowed the operator to control and maneuver the dozer from a safe location, completely out the proximity of danger. The HARD-LINE communications infrastructure was calibrated to extend coverage an additional 2 km via Wifi Sectoral antenna. The next requirement involved reconfiguring the placement of the TeleOp cameras on the bulldozer, which provided optimal viewing angles for the task at hand. Once the system was in place, it took the company approximately three days to successfully excavate the area. After the project was completed, the dozer was reassigned back to the storage barn where both the CAT D8 Dozer and CAT 349 Excavator are still in use. HARD-LINE was able to delivertherequiredhardware to the site 2 weeks after the mine approved the solution. The installation and commissioning took 2 days.
FEEDBACK
The customer was very pleased with the performance of the tele-operated machinery. The application of new strategies will continue to remove people from certain hazards associated with mining, in addition to increases in production. HARD-LINE provided site audits for network assessment and worked together with IT staff to incorporate the required hardware for the wireless network. Also, HARD-LINE supplied all trained service technicians required to implement this project. Full knowledge transfer was provided to ensure all on-site staff were capable of operating and maintaining the system.
CONCLUSION
Mining operations can be made safer by applying tele-operation to the infrastructure of any mine. The technology applied improves mine operations, providing solutions to future challenges, and assists in achieving company goals. HARD-LINE’s expertise and nimble approach to manufacturing combined with a healthy supply of critical spare parts enables a tight turnaround for the client. The goal of protecting personnel from extreme environmental conditions as well as optimizing equipment availability and performance were met.
Disclaimer: The heavy machinery used in this project are products and creations of Caterpillar.
Figure 1. The TeleOp system operating machinery from an ergonomic environment.
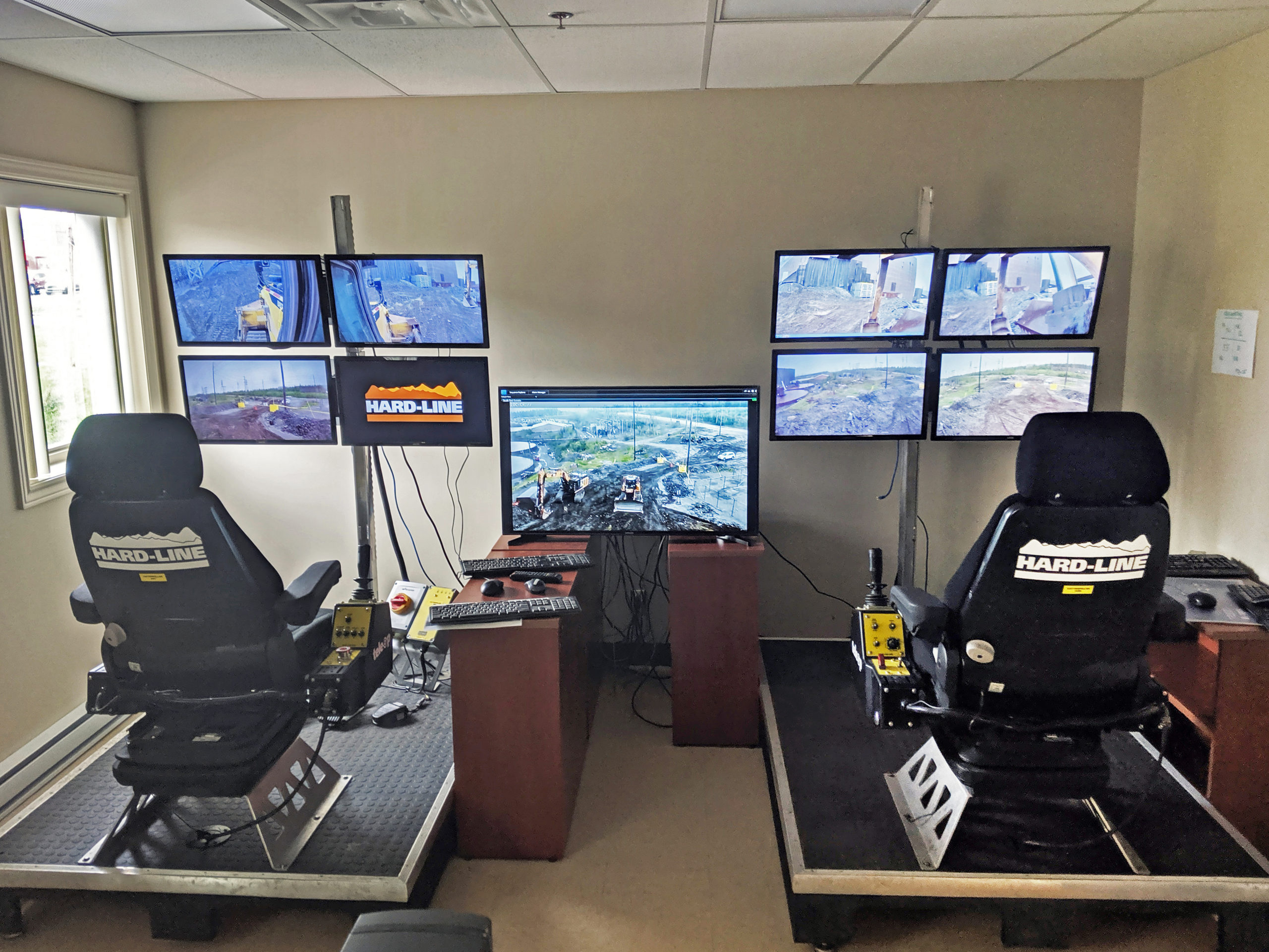
Figure 2. CAT 349 Excavator in front of the ore storage barn.
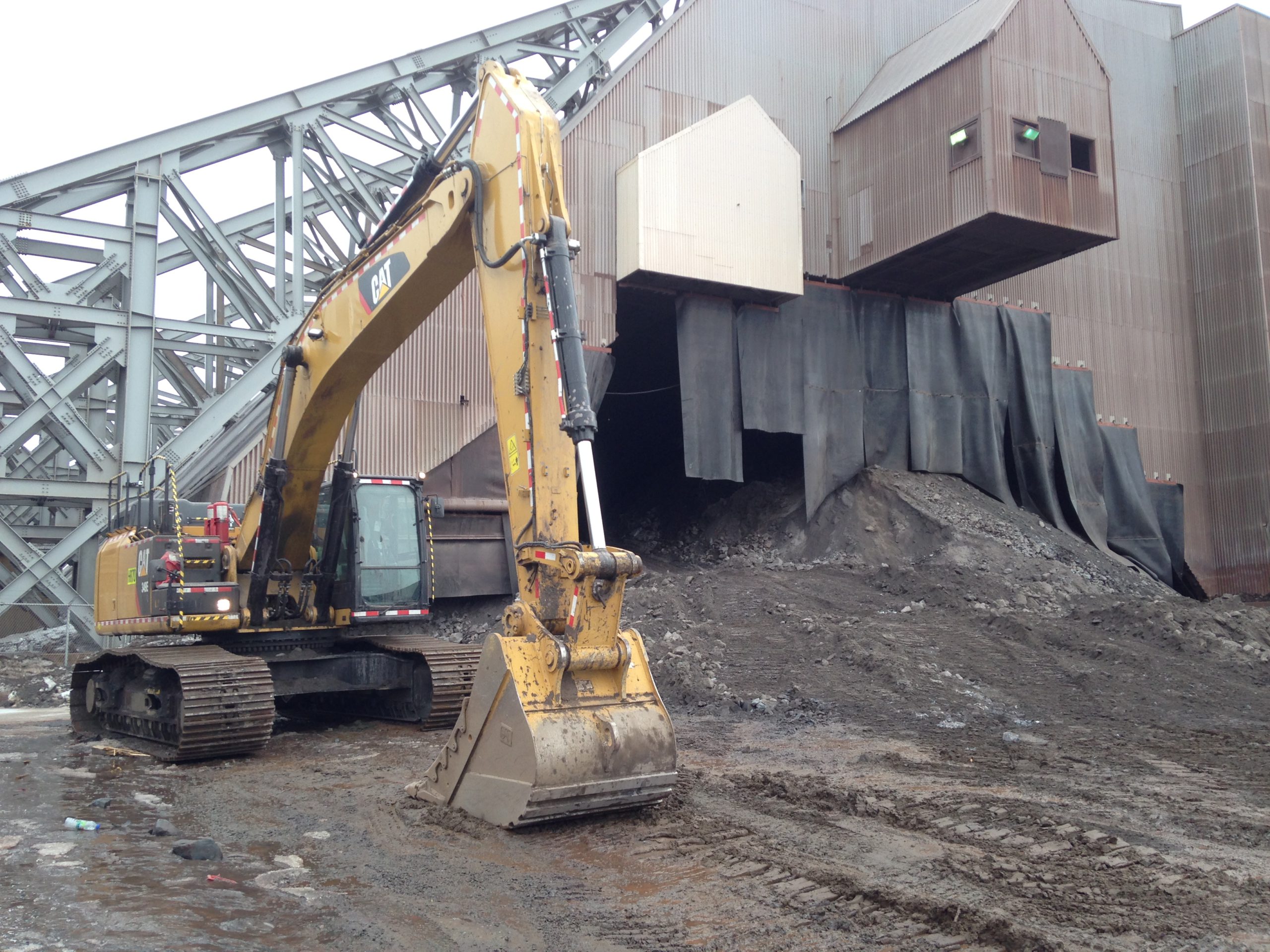