ABSTRACT
The purpose of this case study is to examine the benefits of using Radio Remote Controls (RRC) on a machine retrieval device through an extraction service – reducing downtime while increasing safety in underground mines when equipment is buried. In this study, the remotes used are HARD-LINE’s RRC which allows operation of all types and makes of heavy machinery from a distant location. The retrieval unit is Beltor Engineering’s Mine Extraction Device (MED) MED210 that has a pulling capacity of 210 tons. Beltor Engineering is the Original Equipment Manufacturer (OEM ) of the MED and has been manufacturing this range of dedicated extraction equipment for more than twenty years. When combined, and through the expertise of Murray Engineering’s RetrieveME service – a trained extraction team can remove crushed and / or trapped critical mine equipment like underground mining Load Haul Dump (LHD) loaders and trucks safely from a distance.
INTRODUCTION
HARD-LINE, an international technology company (headquarters in Canada), and Murray Engineering, an Australian mining services provider officially partnered in 2019. Murray provides comprehensive support for HARD-LINE products in Australia, Mongolia, Africa, and the Middle East. This retrieval service is one of many HARD-LINE/Murray collaborations, and for this project an LH621 Loader was buried in rock underground at a nickel mine site in Australia.
APPLICATION
RRC was installed on an MED210 to extract an LHD/Truck that was buried by rocks in a stope. With two Murray Engineering technicians on site, the MED was towed into place 30 metres from the buried vehicle. The MED’s boom was raised as the head plate was positioned against the roof, locking the MED firmly into place. The MED is then attached to the buried machine using a set of rated slings and shackles, which in turn are connected via engineered links to the MED pulling racks. From there, the bridle plate is interlocked onto the teeth of the MED racks, which are then pulled through the MED via two hydraulic cylinders using up to 210T of pulling force. Using RRC, the mining asset is successfully removed at a safe distance for operators. Typically, these extractions are completed in 2 – 5 days depending on underground conditions.
Figure 1. A fully customized RRC Remote was built to use with Beltor’s MED. Below is a recreation of the remotes layout and components.
BENEFITS
There are many benefits when using this method of extraction. Most importantly, this practice eliminates unsafe extractions and minimizes production disruptions. Due to the dangers that come with machine recoveries, the MED is operated remotely from a safe distance of up to 100 metres away with critical data and live video. The risk of injury is significantly reduced even if the retrieval sling fails during operation of the MED. Also, ore production is not compromised as mining equipment can maintain operations while the remote-controlled MED is in use.
Traditional extraction methods use other mining assets like loaders and haul trucks to pull out the buried machine. The uncontrolled movement of the vehicles can present many problems like damage to the mine or the machines, while putting operators and spotters at far greater risk. The typical process is uneconomical, normally interrupting production for weeks compared to only a few days with the remote operated MED.
“
THE REMOTE BELTOR MACHINE EXTRACTION DEVICE IS A GREAT, COMPACT ‘EASY TO USE’ UNIT WHICH MAKES THE RETRIEVAL PROCESS MUCH MORE STREAMLINED AND EFFICIENT.
IN ADDITION TO THE SMOOTH, PROPORTIONALLY CONTROLLED ACTION OF THE REMOTE, IT ALSO INCLUDES TILT AND OPERATOR-PRESENT FUNCTIONALITY TO GIVE ADDED PROTECTION FOR THE OPERATOR AND OTHERS IN THE WORK AREA.
DURING THE OPERATION OF THE MED, THE OPERATOR CAN STAND UP TO 30M AWAY FROM THE MED IN LINE OF SIGHT, WITH OVER 100M BETWEEN THE MED AND THE TRAPPED MACHINE, WHICH ELIMINATES POTENTIAL HAZARDS AND MAKES THE RETRIEVAL A SAFER PROCESS FOR ALL PERSONNEL. “
BEN ROBINSON, BELTOR EXTRACTION SPECIALIST, MURRAY ENGINEERING
The RRC unit is equipped with a digital display showing key data including the amount of force being applied. With the RetrieveME service, no remediation to the mine is required and there is no additional damage to the mining asset after successful retrieval. This service is available at a fraction of the cost of replacing an entire machine.
CONCLUSION
Mining equipment is built to extract ore, not to extract mining equipment. Murray Engineering’s MED, which includes HARD-LINE’s industry-leading remote controls and Beltor’s MED, provides underground mine sites with a retrieval service that reduces costs and increases safety. This service has been used frequently in underground mines all over Australia.
Figure 2. Mine Extraction Device (MED) converted for use with HARD-LINE’s Radio Remote Control (RRC), equipment operator shown on the left.
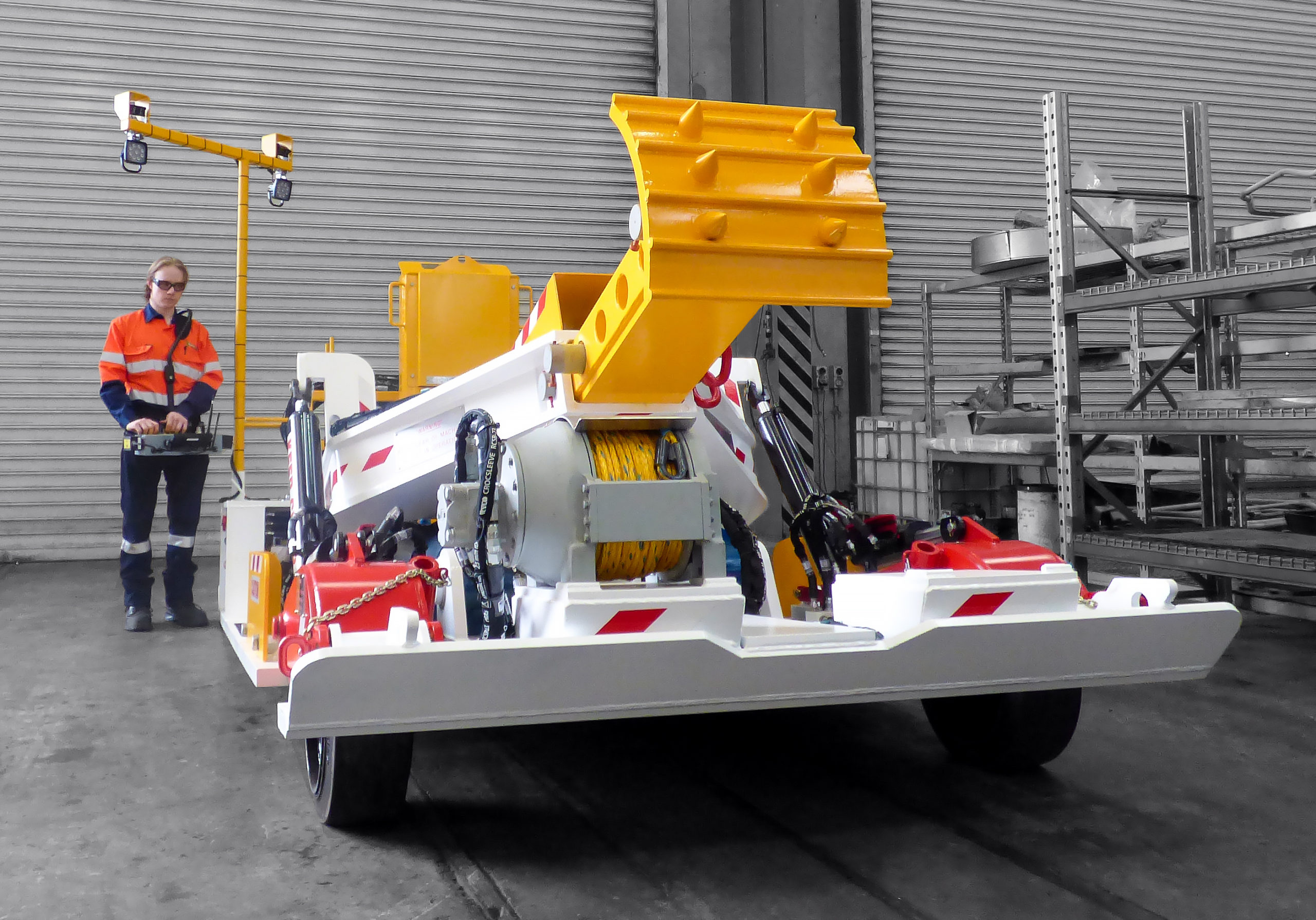
Figure 3. View of Beltor’s MED with the operators underground, in the process of retrieving the LH621 loader in Australia.
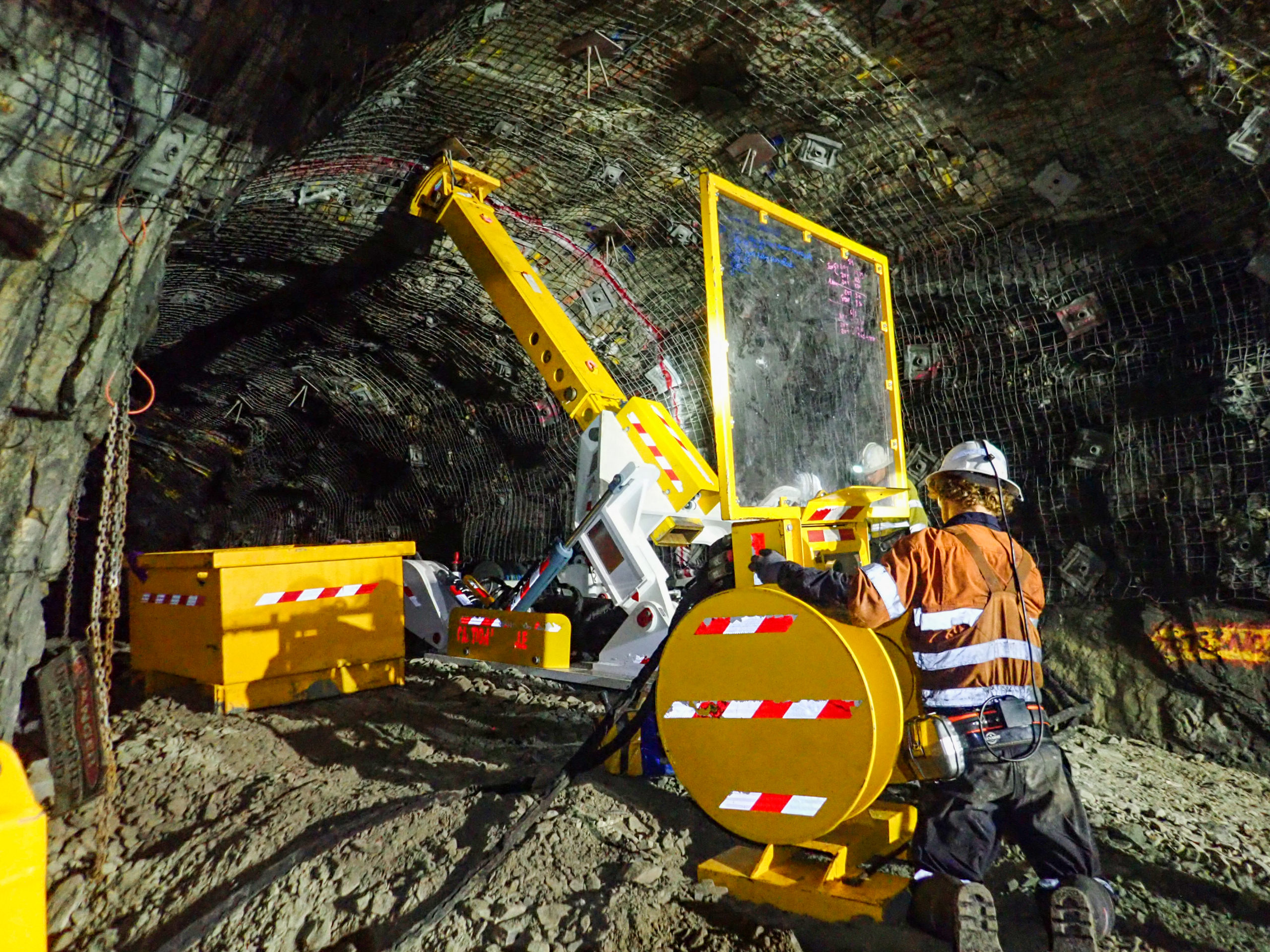