OVERVIEW
Private and public entities that deal with transportation and public works explore different ways to maximize labor efficiencies while optimizing costs. Some challenges include the clearing of culverts and drainage systems which are often congested with rock, dirt, and other debris blocking pathways for water to flow. The removal of these objects can be costly, labor-intensive, and dangerous. Working in culverts can present a real challenge due to issues associated with confined spaces. Various machines and methods are used, however; HARD-LINE’s LP401 provides the best overall benefits. The low-profile skid-steer loader is controlled remotely; which allows the operator to remain out of harm’s way and complete work as safely and effectively as possible.
CLIENT
Based in Phoenix, Arizona, this reputable company is a civil infrastructure firm that has worked on hundreds of municipal, state, and federal infrastructure-related projects in heavy/highway construction in the state for the past 30 years.
APPLICATION
This Phoenix-based company has taken different approaches when clearing culverts including shoveling by hand, applying high-pressure spray systems, using vac trucks (vacuum tankers) and most recently and most effectively employing heavy equipment enabled by remote-control technology.
This company was tasked to clear six highly clogged box culverts full of sand and rubble. The debris stood between 2-to-3 feet in height nearly halfway up the 5-foot cement box culvert. The interior dimensions were 60 inches tall, 132 inches wide, and 125 feet long, running north to south under the Sun Valley Parkway northwest of Phoenix. For this project, a HARD-LINE employee was onsite and documented the effectiveness of the LP401.
Work on the project began at 6:30 a.m. as a crew of four employees began piling and removing large heaps of culvert blocking material. One employee operated the LP401 via remote control, removing up to two loads a minute. Another worker operated a large articulated loader. He was tasked to sculpt the downstream river bed and remove the accumulated sand and debris into the dump truck. Two additional workers kept the dust down and drove a dump truck.
RESULT
As a fully radio-remote controlled unit with a low-profile body built to access confined spaces, the LP401 was able to quickly and efficiently complete the project. The multi-purpose vehicle travels 6 mph and has a lifting capacity of 2000 lbs (907 Kg) and a one-half cubic yard (1/2 yd³) bucket.
Using the LP401, this cleaning project took on average 2 hours per culvert which translates to 12 hours overall. A calculated 124 cubic yards of sand, rock, and trash were removed from the stream resulting in an average removal rate of 10.5 cubic yards per hour.
To appreciate the significance and capacity of the HARD-LINE LP401 versus the competition, this case study explores the findings of a 2014 Ohio Department of Transportation report, Evaluation of Box Culvert Maintenance Methods, wherein the authors make the argument in favor of the adoption of radio-remote-controlled tools over methods of manual labor and vac truck. In this report, a HARD-LINE competitor for culvert cleaning is used. The LP401 was not involved in the ODOT report.
With the competitor’s top speed of 0.9 mph and a bucket capacity of only a quarter of a cubic yard (1/4 yd³), our estimates show that if it was used on this project, the unit would make twice as many trips as the LP401. The competitor’s bucket holds half as much and travels at a slower speed (0.9 mph vs 6 mph). Each trip into the culvert would take at least 6 times as long. Extrapolating the technical specification information provided by the manufacturer we find that the competition, if used on the project would have an estimated completion time of 144 hours clearing 0.86 cubic yards per hour. Our competitor’s Adjusted Project Completion Hours is calculated at approximately 144 compared to the LP401’s at just 12 hours.
CONCLUSION
Methods of culvert cleaning that move less material at lower speeds, like manually directing high-pressure water, vacuum hoses, and lower functioning machinery, ultimately put more strain on workers and wear on equipment. With an average operating crew cost of $1200.00 per workday on the project we studied (according to DOT reports and anecdotal evidence) the LP401’s efficiency can greatly reduce labor costs and time. Time saved on these projects would allow for other necessary work to be accomplished like slope mowing, post-hole drilling, snow blowing, slope vegetation management, and other outdoor-related tasks.
The increase in efficiency by the LP401, when compared to other methods, allows for preventative instead of reactive maintenance strategies to be implemented on local waterways, thus avoiding floods and in turn being better stewards to our environment. The LP401 is not only safe, it also provides significant operational budgetary savings compared to vac trucks and other remote-control units. Increased productivity, reduced project costs, and enhanced efficiency makes the LP401 the best choice for culvert preventative maintenance and cleaning.
Figure 1. A 5-foot high cement box culvert largely obstructed by dirt and debris.
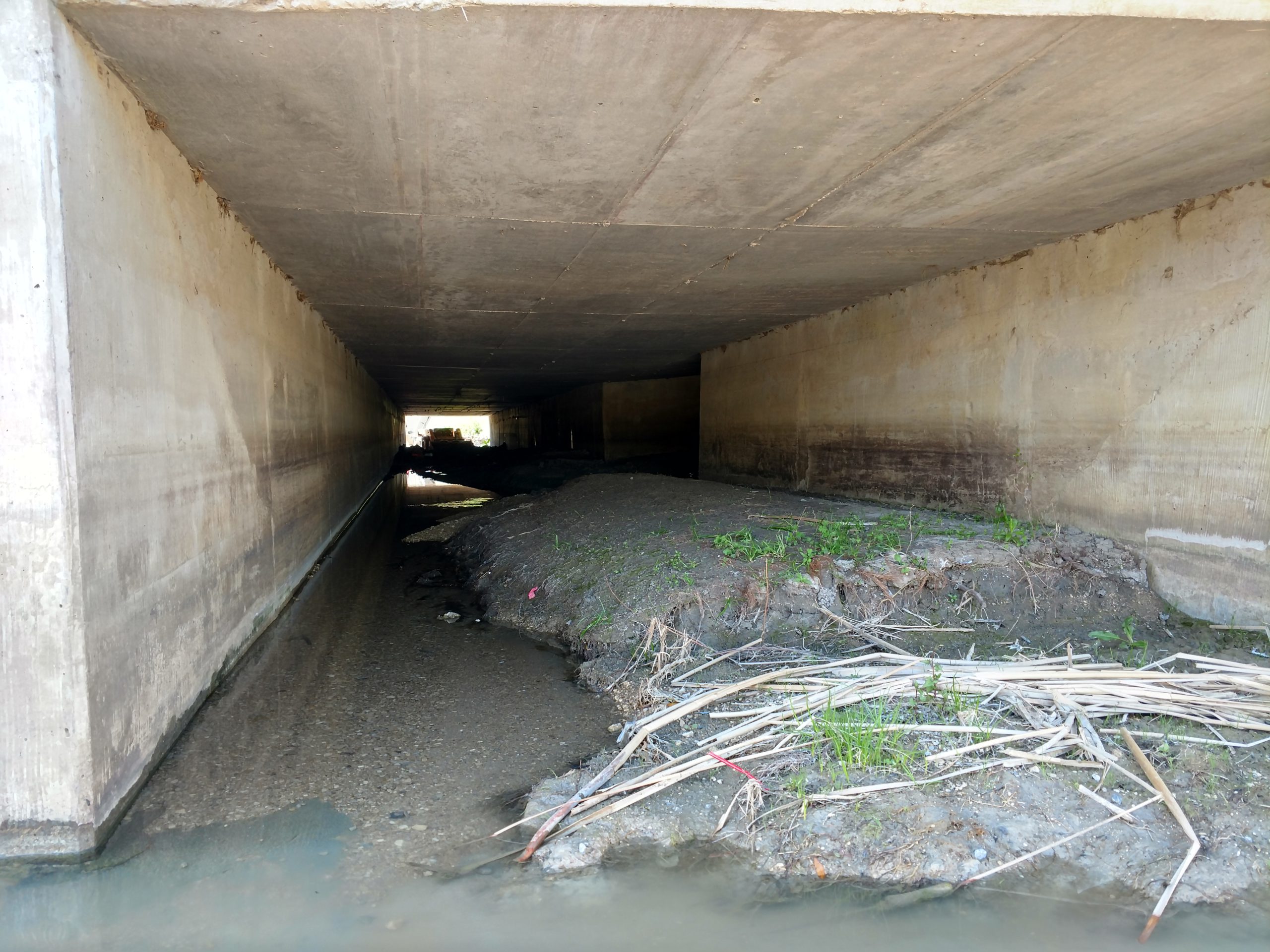
Figure 2. The LP401 lifting a heavy obstacle.
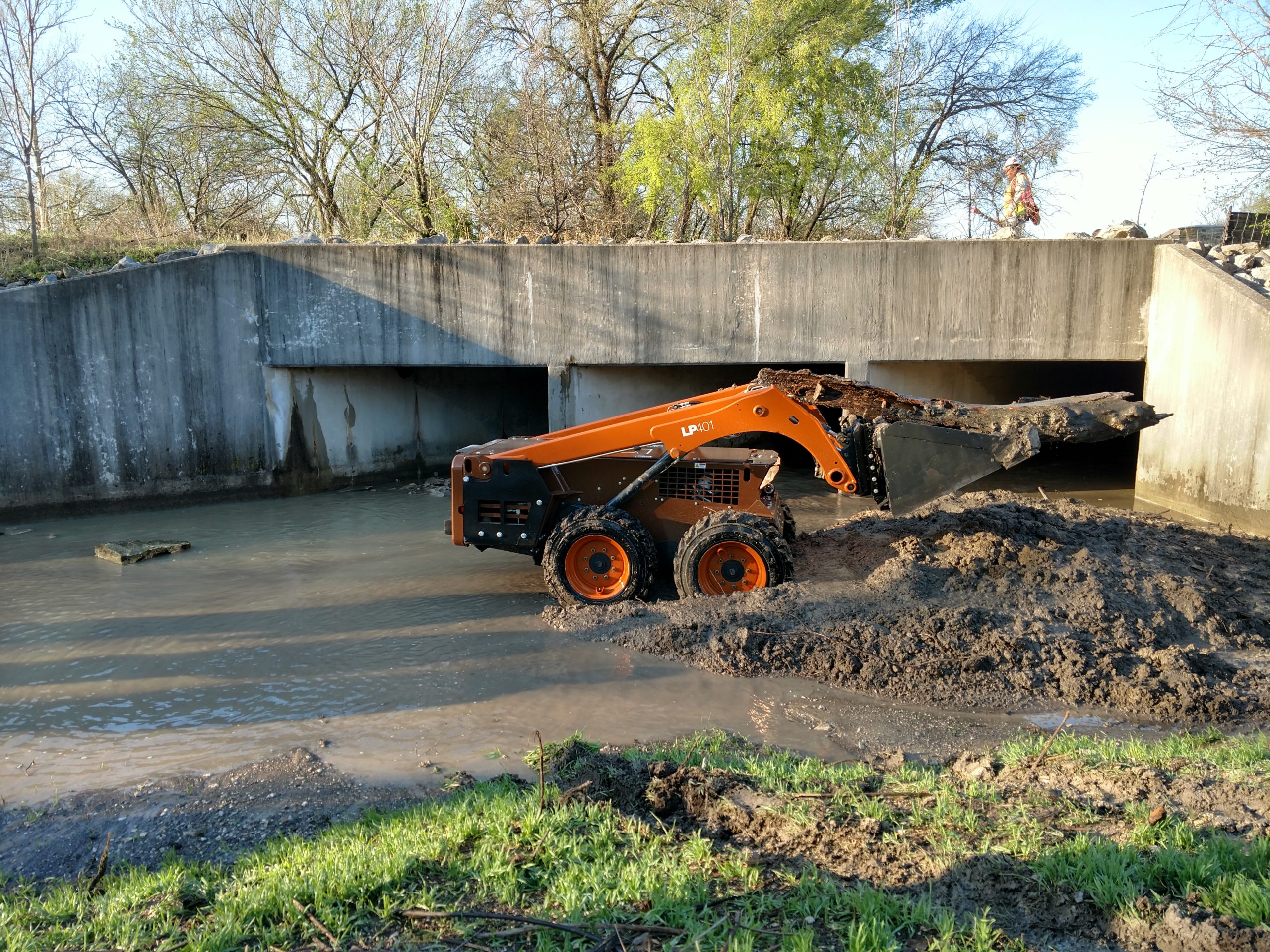